Time, Talent & ROI: Offshore Workforce Planning Mistakes to Avoid
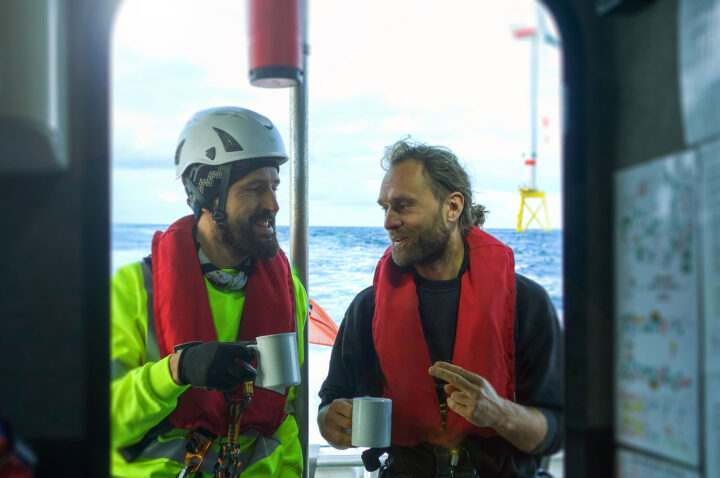
Across offshore wind, dredging and marine construction, there’s no such thing as a “small” planning mistake. A single error—like assigning the wrong person, missing documentation, or misjudging skill levels can have serious, even fatal, consequences.
Whether it’s a jack-up barge in the North Sea, a trailing suction hopper dredger in Southeast Asia, or a cable lay vessel off the UK coast, crews rely on accurate, real-time planning to stay safe and compliant. Yet, many organisations still overlook workforce planning as a key lever for efficiency and risk reduction.
As compliance expectations tighten and ESG pressures grow—particularly in high-visibility sectors like offshore wind—outdated planning methods put both lives and margins at risk. Rotations, crew readiness, and qualifications can no longer be managed through disconnected spreadsheets or siloed systems.
Below are the five most common offshore workforce planning mistakes we see and how you can fix them now.
1. Using spreadsheets to schedule crews
If you’re still managing crew rotations in spreadsheets, you’re setting yourself up for failure. Manual tools can’t keep pace with the speed and complexity of offshore work. Especially for project-based operations in wind farm installations, subsea construction, or large-scale dredging projects.
Every time someone updates a sheet, the risk of errors increases. Schedulers lose hours checking and reissuing data, while compliance teams struggle to validate skills and documentation.
Real-world impact: Overstaffing, poor crew allocation, and compliance failures. At best, this leads to wasted costs. At worst, lives may be put in danger, and reputations suffer.
✅ Fix: Switch to automated planning tools that offer real-time visibility, dynamic rostering, and compliance alerts. A digital platform can surface risks before they become problems.
2. Overstaffing to compensate for uncertainty
Many operators over-crew jobs to avoid skill gaps, but this quick fix comes at a steep cost. Without clear visibility into who is trained, qualified, and available, managers often add headcount “just in case” – especially on fast-moving offshore scopes.
That approach erodes margins and drives up fatigue-related HSE risks.
Real-world impact: Burnout, higher mitigation costs, and missed productivity targets.
✅ Fix: Use historical and current data to forecast demand and plan staffing levels accurately. A good planning system helps you allocate the right number of crew with the right skills—no more, no less.
3. Missing certification data at the worst time
Sending someone offshore only to discover they’re not certified wastes time and money—and creates major compliance risks.
Many operators still rely on scattered documents, inbox searches, or even memory to validate certifications.
Real-world impact: Failed audits, unqualified workers on-site, costly crew swaps, and third-party contractors brought in at the last minute.
✅ Fix: Centralise certification and competency tracking in a unified system like OneView. When everyone uses the same trusted platform, teams can validate compliance instantly.
4. Lack of real-time visibility hurts decision-making
Offshore operations change fast- weather windows open and close, equipment shifts, and scopes change. If your workforce data lags behind reality, your ability to adapt disappears. Without real-time insight into who’s on-site, what they’re certified to do, or where coverage gaps exist, you’re managing blind.
When teams work in silos, crew movement becomes slow, inefficient, and risky.
Real-world impact: Delays, duplicated effort, unplanned downtime, and missed opportunities to optimise resources.
✅ Fix: Connect your workforce planning tools with operations. A unified, real-time view lets everyone—from schedulers to HSE leads—work from the same source of truth and act quickly when things shift.
5. No ROI tracking means you’re flying blind
If you’re not measuring workforce planning ROI, you can’t improve it. Many organisations rely on gut feel or outdated metrics, missing valuable insights into what’s working and what’s not.
Without clear benchmarks, you risk over-allocating resources, wasting training budgets, or overlooking systemic risks until it’s too late.
Real-world impact: Unknown costs, inconsistent outcomes, and poor strategic alignment.
✅ Fix: Build a workforce planning framework that ties every staffing decision to business impact—whether it’s reducing vessel downtime, avoiding compliance penalties, or improving crew retention.. Smart scheduling software should help you generate reports, track KPIs, and continuously improve planning decisions.
👉 Take the Assessment to uncover gaps, risks, and improvement opportunities in your offshore workforce strategy.
Want to see how a platform like OneView can bring visibility, control, and ROI to your offshore workforce strategy?
Author:
Lee Clarke, OneView director
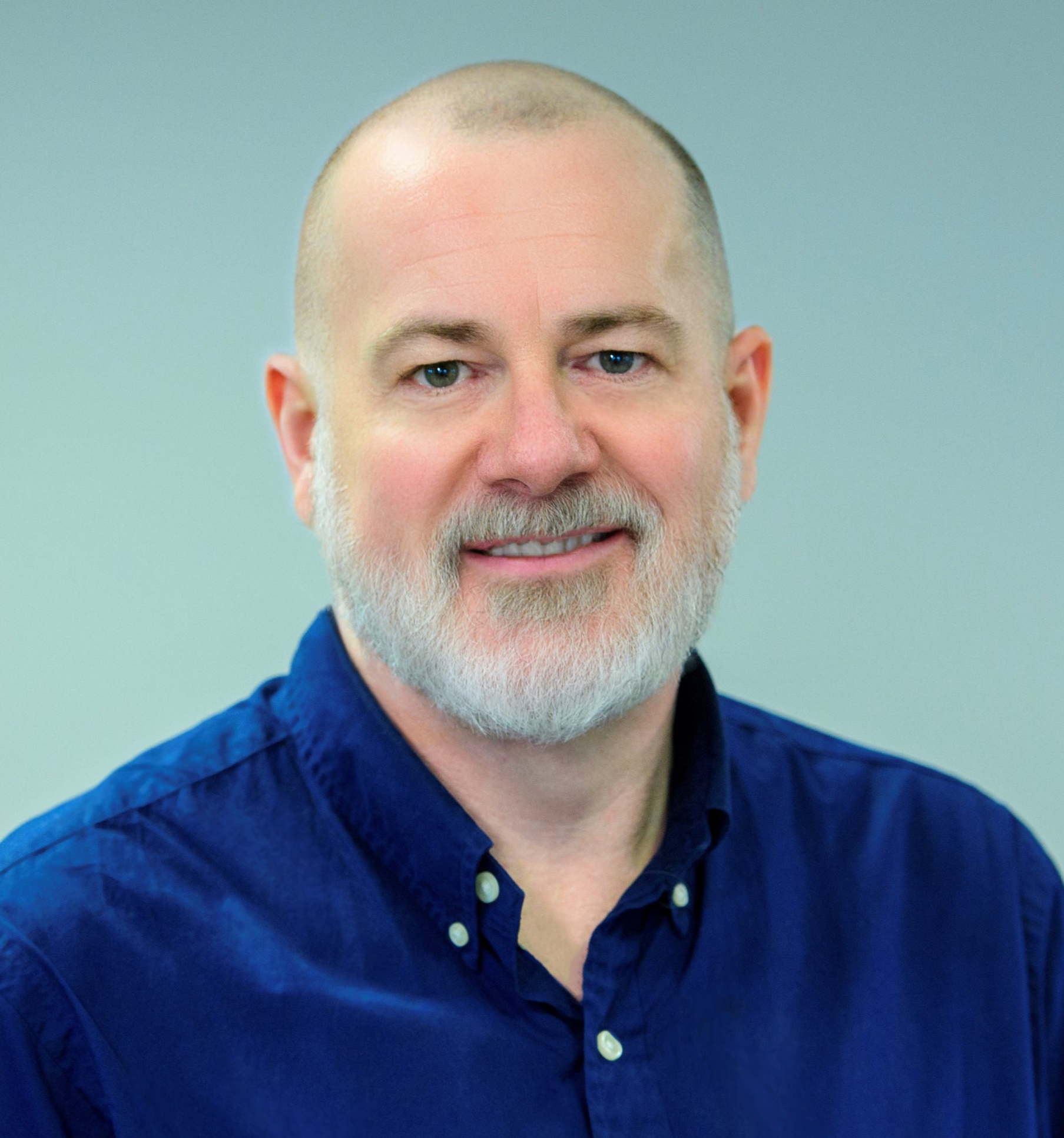